Fuchs Consulting, Inc. has developed a BRIDGE VIRTUAL ASSEMBLY SYSTEM (BRIDGE VAS) that
improves manufacturing processes and enhances quality control for steel bridge fabrication.
The system replaces conventional match-drilling with virtual assembly methods, creating
custom-designed splice plates. Vastly improved measurement and documentation of fabricated
girders is possible with the system.
| |
System Applications
- Virtual Assembly Tool
- Create custom-made splice plates without a physical laydown
- Precise splice hole location measurements
- Measure full-sized holes and produce CAD drawing for splice plate
- Simulate fit-up of girders without shop assembly
- Quality Control Tool
- Fabrication documentation
- Permanent, traceable, certifiable record of fabricated girder
- As-built girder dimensioning
- Overall size and shape of girder
- Camber, sweep, length, end-kick, other measured dimensions
- Compare with CAD design
- Catch fabrication problems on-site prior to painting
- Protect against disputes (documentation that girder was fabricated as designed)
| 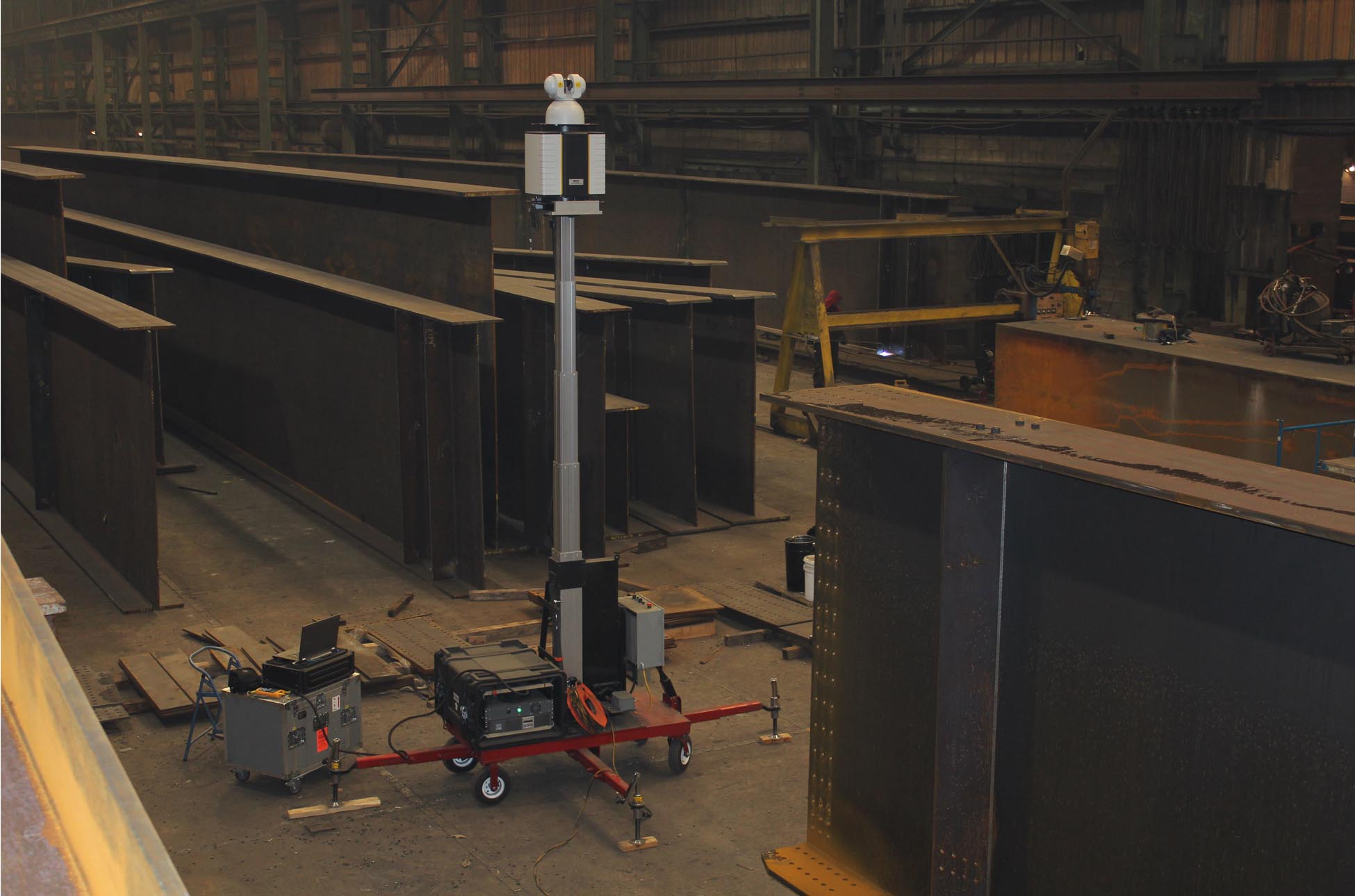 |
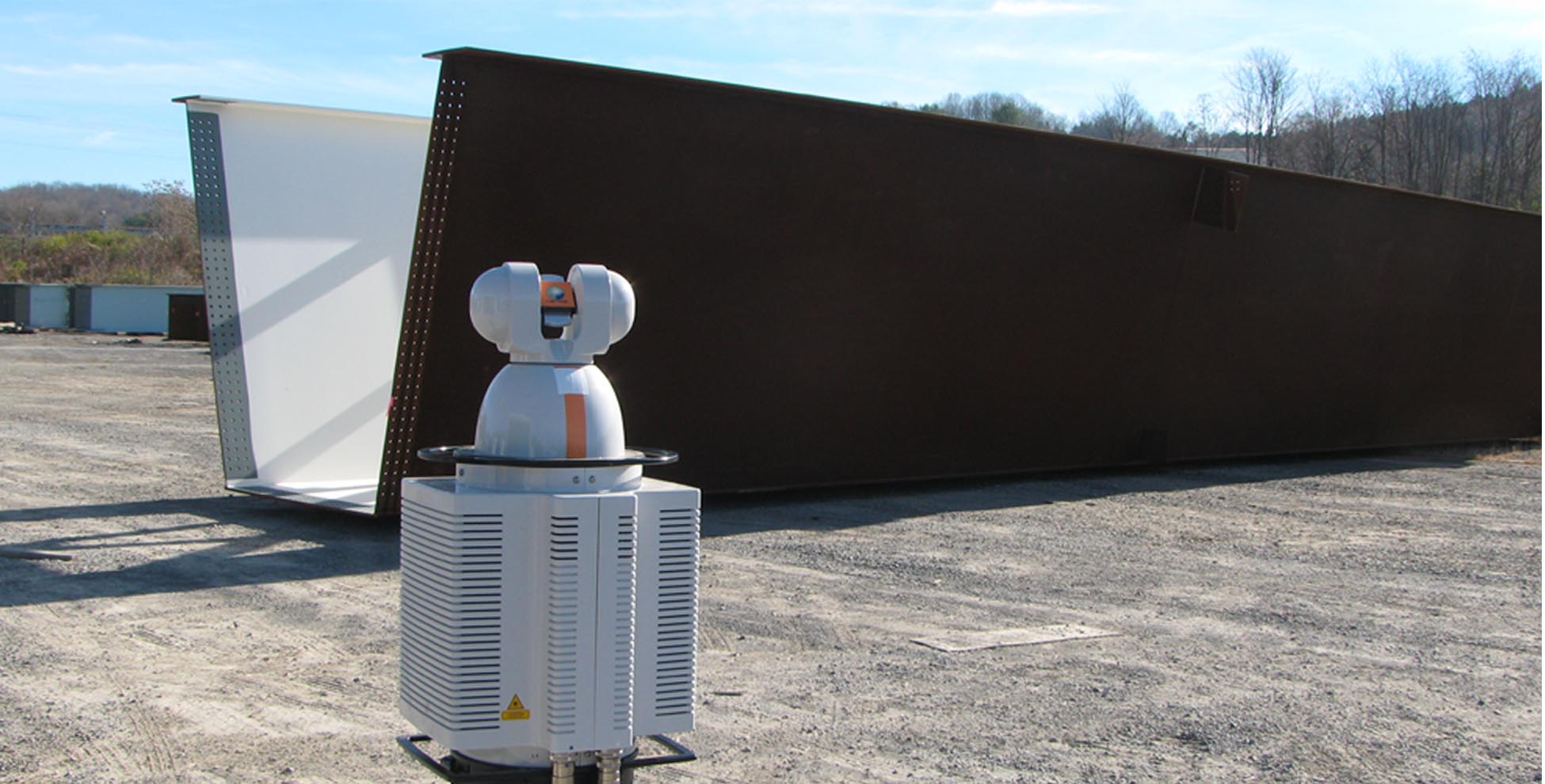 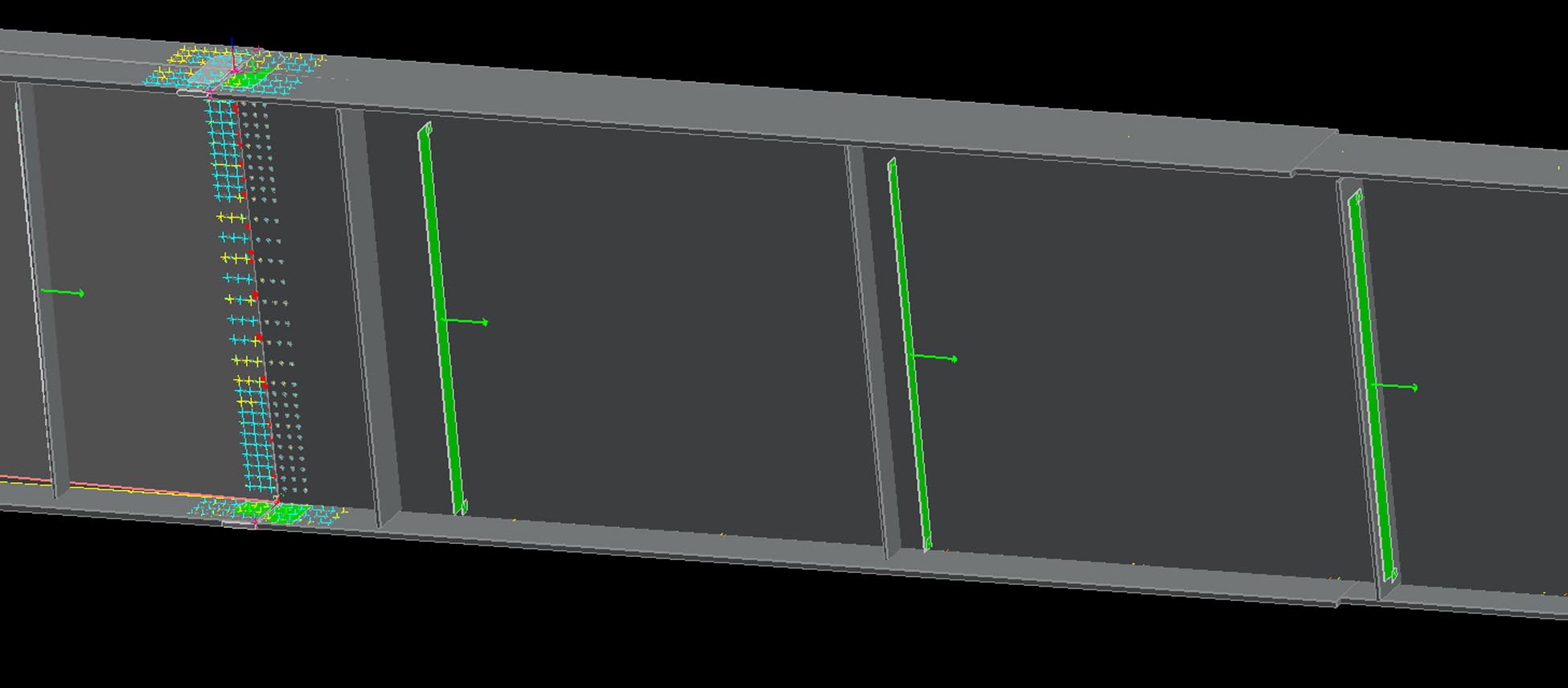 |
System Features
- Fits in a common steel fabrication shop with minimal changes
- Can work in harsh shop conditions (dust, debris, vibrations, temperature)
- Is not designed to work in only the most advanced shop
- Does not require dedicated work space/special measurement room
- Does not require special gantry or major capital investments to deploy the equipment
- Is capable of measuring the full range of girders and components to be fabricated
- Highly flexible, mobile system
- Standard plate girders, curved girders
- Large haunched, tapered girders
- Tubs, boxes, very complex parts
- Use in the shop or in the field
- Makes automated measurements
- Easy-to-operate
- Measure directly on a specimen
- Does not require manual operator measurements or intervention
- Can measure an entire girder without repositioning the girder during measurement
- Works with existing processes
- 3D CAD models from 2D shop drawings
- Direct output to CNC drilling machinery
|
Potential Benefits
One of the main advantages of the BRIDGE VAS is to improve the manufacturing process by
eliminating some time-consuming steps. By virtually piecing together the individually
measured girders, the need to physically laydown, align, and match-drill spliced pairs
can be eliminated. The match-drilling component of fabrication is a bottleneck in the
overall process and the elimination of this step improves fabrication as a whole.
Using software tools, girders can now be virtually manipulated and aligned and the
operator can produce a combined camber diagram of a girder pair or of multiple girders.
The second main advantage of the BRIDGE VAS is that it provides substantially more
documentation than currently exists and provides access to types of information that are
not currently available. Providing accurate information on what is being made in a shop,
in an easily interpretable and useful form, can dramatically improve the quality of the
end-product produced.
| 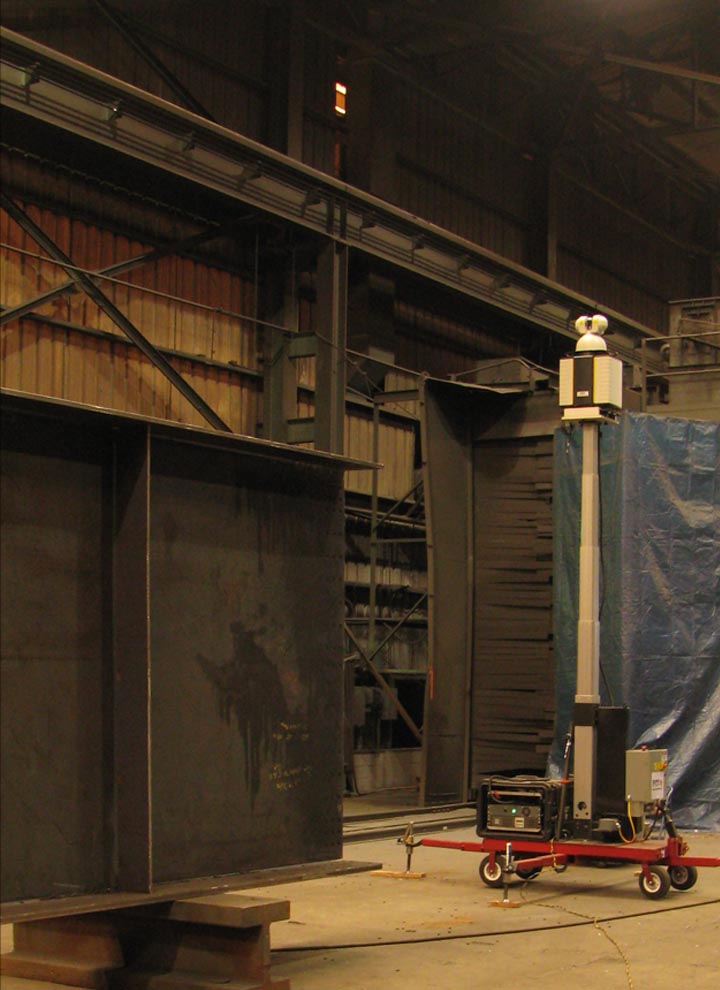 |
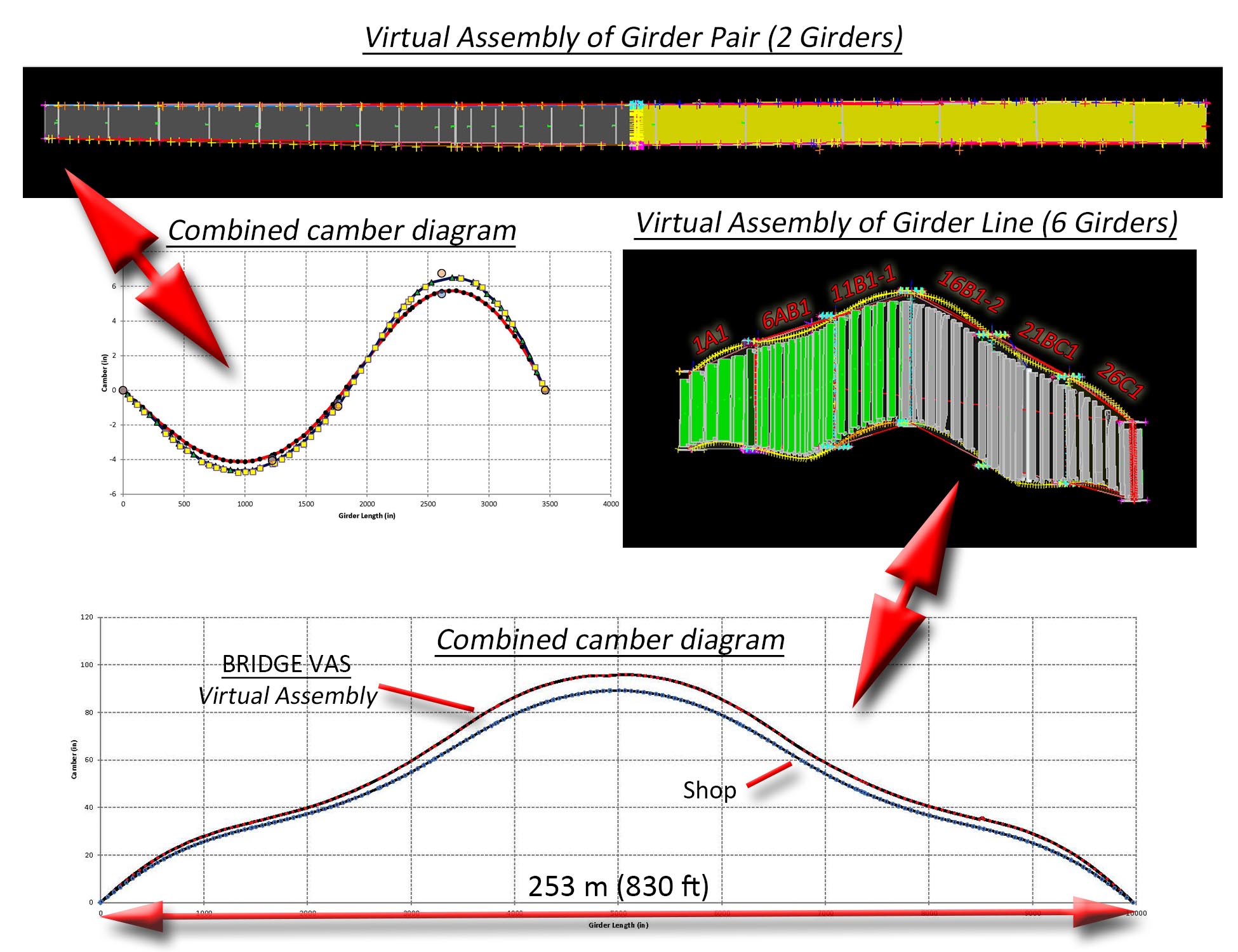 | |